Muddy Boots – The first Food Safety & Quality Management system certified by HACCP International.
Greenlight Quality Management (GLQM) by Muddy Boots was the first cloud-based Food Safety & Quality Management system to carry the HACCP International certification mark. The all-in-one solution is used by food manufacturers, food processors and suppliers to ensure the efficient, accurate and secure management of safe food, product quality and Compliance across operations.
The system can be configured to the seven principles of HACCP to effectively track, report and manage known or potential issues. With systemised procedures you are in control of your processes and assured that issues are being actioned in a timely manner.
“The globalisation of food production and trade has created a complex supply chain, resulting in a high demand for food producers that are clean, green and provide safe food. The importance for companies of upholding and building on food safety, traceability and quality concerns that dominate consumer attitudes cannot be overstated and has become even more prevalent during the recent global events brought on by Covid-19.” Sean Verlander, Senior Business Development Manager, Muddy Boots.
Muddy Boots GLQM: The Benefits:
Integration made easy
GLQM seamlessly integrates with ERP, hardware devices and third-party data sets including cold chain management, planning solutions, barcode scanners and temperature probes.
Real time reporting, allowing immediate action
Configurable reporting capabilities and escalation processes enable you to share reports automatically by site, supplier, product, process or people. Non-conformance issues or corrective actions can be resolved quickly through a robust escalation management process that includes responsibility being automatically assigned and photographs attached as evidence. Notifications are automatically sent to relevant parties with each corrective action tracked to closure with a verifiable audit trail.
Mobile checking without boundaries
Check at any point in your supply chain: intake; production; dispatch or on the shop floor. The easy-to-understand red, amber and green system flag communicates results including verification of completed procedures, changes in critical control points and discrepancies in critical limits.
Ease of use
The mobile app displays images and textual guidance for each task/check, presenting operators with a visual display of what good looks like at the tap of a button.
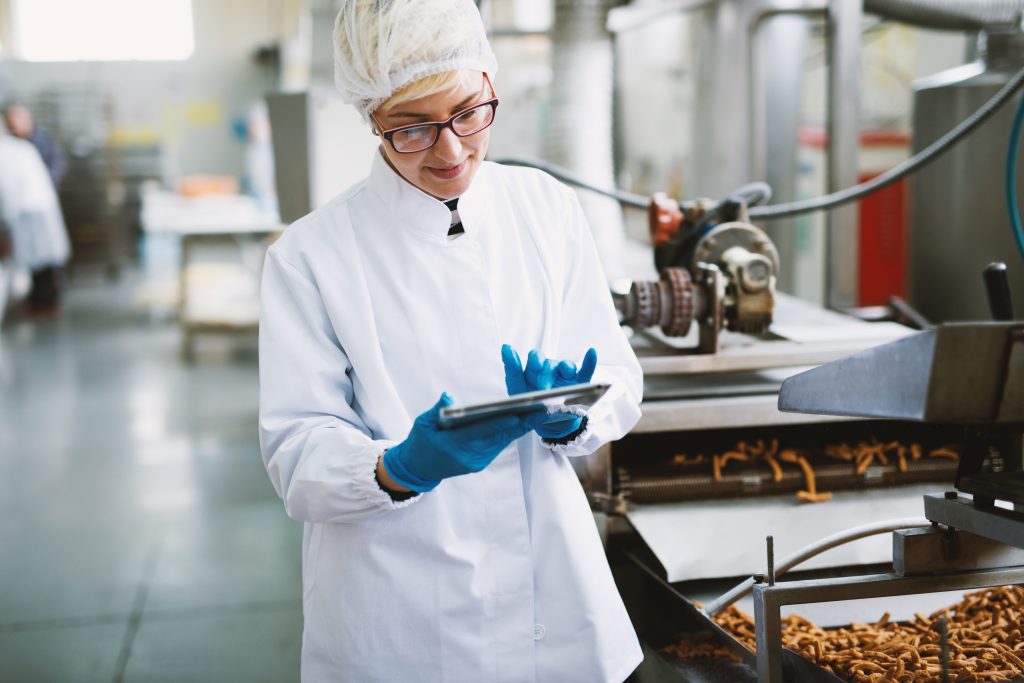
Young female worker in sterile clothes is checking quality of products in food factory.
Task scheduler
A seamless two-way communication flow between management and operators. Tasks can be scheduled to be carried out at a given time or frequency. Operators are prompted to carry out these tasks, with alerts sent to managers if not completed.
Build assessments quickly
Advanced reporting provides absolute visibility and insights into the performance of site, products, suppliers and people. A powerful tool for benchmarking and preparing for audits. Business intelligence analytics produce dashboards to identify where problems are occurring, recognise trends and profile performance over time.
Data Integrity
Records in the Muddy Boots platform are automatically date and time stamped, certifying verified and accurate data. The platform enables you to safeguard your reputation by being able to demonstrate your ethical, social, environmental and or sustainable credentials and compliance standards.
Karen Constable, Technical Manager HACCP International explains “Muddy Boots is suitable for food manufacturing and food handling operations on a global scale, the system features ‘fail safe’ characteristics, data integrity features and record verification functions, with an excellent corrective actions manager.”
Take control of your product quality
Mr Clive Withinshaw, Director HACCP International commented, “Greenlight Quality Management impressed our evaluation team with its ability to handle complex food safety system requirements within a simple, user-friendly interface. The system encourages and supports operators to perform their tasks properly, and provides all the information that quality and food safety managers need in a secure and easy-to-access format.
A single data set presented in real-time provides a clear picture of operations and inefficiencies, enabling prompt decisions based on accurate and up to the minute information and significantly improving response times.
The real-time visibility of the GLQM solution provides greater transparency and traceability to track facilities, safe food-handling, product quality, preventative maintenance, etc. A single solution to efficiently manage day to day processes and any disruptions”.
For further information on Muddy Boots and Greenlight Quality Management,
Visit the Greenlight Quality Management page or request a product demonstration
Contact number: UK +44 (0) 1989 780540 or email sales@muddyboots.com